High Frequency Welding Machine
Principles and Advantages of High-Frequency Welding Machines
High-frequency welding machines have become a popular choice across various manufacturing sectors thanks to their ability to effectively bond soft plastic materials. In particular, for products made from PVC or PU—materials commonly used in both industrial and consumer applications—high-frequency welding is almost essential. This technology is frequently used in the production of items such as tarpaulins, field tents, canopies, outdoor advertising banners, inflatable boats, blood bags, waterbeds, conveyor belts, drip irrigation systems, and raincoats.
How High-Frequency Welding Works and Its Key Advantages
Fundamentally, a high-frequency welding machine operates by generating heat within the material through an electromagnetic field. When the material is placed between two electrodes and subjected to high-frequency voltage, the molecules inside the material begin to oscillate intensely, generating internal heat. This heat softens the material and initiates melting. When the two material layers are pressed together under the influence of high-frequency current, they fuse into a strong, cohesive bond capable of withstanding significant tensile force without peeling or tearing.
Notable Advantages of High-Frequency Welding
One of the key advantages of high-frequency welding is its speed. Within just a few seconds, the material is heated from the inside and securely bonded, significantly reducing processing time in production lines.
Compared to conventional welding methods such as thermal wire, hot air, or infrared radiation, high-frequency technology presents clear benefits. Traditional methods apply external heat that must penetrate the material before it can melt the bonding surface. This often risks overheating the material surface, leading to deformation, scorching, or compromised weld quality.
The effectiveness of high-frequency welding also depends on the type of material used. Thermoplastics like PVC and PU respond well to high-frequency electromagnetic fields, making them highly suitable for this technique. Conversely, materials like PE generate insufficient internal heat when exposed to high frequency, making them largely ineffective for this method.
How to Determine Whether a Material Is Suitable for High-Frequency Welding
To determine whether your material is compatible with high-frequency welding technology, the most critical factor is its responsiveness to high-frequency electromagnetic fields.
Specifically, the material should have a high dielectric loss factor, meaning its internal molecules can oscillate and generate heat when placed in a high-frequency field. Thermoplastics such as PVC, PU, and TPU are well-suited because they easily generate internal heat and produce strong welds when exposed to high frequency. On the other hand, materials like PE, PP, or PTFE are more difficult to weld using this method due to their poor dielectric heating characteristics.
The simplest way to verify compatibility is to contact the equipment supplier to test a sample or to request the material’s dielectric loss factor from the plastic manufacturer. If the value is low, the material is not suitable for high-frequency welding.
Does Input Voltage Affect Weld Quality?
Absolutely. Input voltage plays a critical role in the quality of high-frequency welds. Each welding machine is designed to operate within a specific input voltage range to achieve its rated power output and maintain a stable high frequency. If the voltage fluctuates excessively, the machine may fail to generate sufficient electromagnetic energy, resulting in the following issues:
The weld joint may not reach the required internal temperature, causing incomplete or uneven bonding.
Frequency instability may occur, reducing the durability of the weld.
Over-voltage or over-current protection may trigger, interrupting the production process.
For instance, the Danrel DR‑8KW high-frequency welding machine requires a three-phase 380 V power supply to achieve an 8 kW output and a stable frequency of 27.12 MHz, as accurately listed on EMIN. If the input voltage drops more than ±5% from the specified value, actual power output will decrease, directly affecting weld quality in products such as tarpaulins, raincoats, or inflatable boats—where weak or gapped welds may occur.
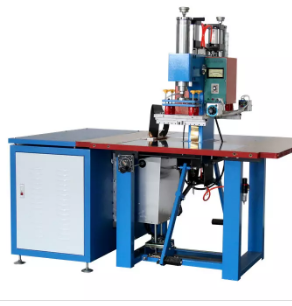
See more at: Danrel high frequency welding machine
Recommended Solutions
Use a high-quality voltage stabilizer or transformer to maintain consistent input power if the local supply is unstable.
Regularly monitor the input voltage during operation and maintain it within the range of 360 to 400 V to ensure optimal welding performance.
-
-
-
-
-
-
-
-
-
-
-
-
-
-
-
-
-
-
-
-
-
-
-
-